News Archive
Dec152016Season’s Greetings From Amber Industries
We would like to take this opportunity to say a thank you to all of our staff, stakeholders, suppliers, partners and customers for your support during 2016. We are looking forward to 2017 and working with all of you next year. Season’s greetings from all of us and we wish you a happy Christmas and a prosperous New Year.
Opening Hours during the holiday period
23 December 2016 08:30 - 14:00
24 December 2016 to 02 January 2017 - Closed
03 January 2017 onward's 08:30 - 17:00
We have had an excellent year over the last 12 months and are pleased to be moving into the next year with a full order book. We have significant expansion plans for 2017 and more news will be made available in this area over the first months of the year. We look forward to working with you on your conveyor projects both in the UK and abroad in our export markets.
Nov142016Who Are......Amber Industries
UK Conveyor designers, manufacturers, installers, controls, service and spares - Providing products, systems and solutions to many industries throughout the UK and worldwide.
Amber Industries is a primary UK designer, manufacturer and supplier of conveyor equipment and systems with over 40 year's experience in the automated mechanical handling and conveyor industry.
To many of our clients the safe, timely and cost effective movement of goods through their facilities is critical to their businesses. Amber Industries Ltd’s mission is to enhance the efficiency of our client’s operations through the provision of innovative and expertly tailored conveyor solutions at a competitive price.
Sep272016IMHX Generates Enquiries For Amber Industries
Amber Industries Ltd, a major UK conveyor systems manufacturer exhibited last week at the IMHX 16 event at the NEC, Birmingham, where professionals from the materials handling and logistics sectors gather to see displays of the latest innovations in plant and equipment for their industry.
Amber Industries stand showcased a carton & tote handling conveyor system and a pallet conveyor system. The carton & tote handling conveyor systems incorporated a 90 degree powered belt curve which transferred boxes onto a length of lineshaft powered roller conveyor including a powered roller curve. This then fed onto a section of 24V zero line pressure (ZLP) conveyor, which was zoned in order to separate the boxes and prevent them from touching each other; this being a particularly useful feature of ZLP conveyor systems for applications where fragile packages are being handled and for picking line conveyors.
The pallet conveyor system consisted of pallet modules which indexed a standard pallet between two positions. The simplicity of the design and the smooth movement of the pallet between positions was remarked upon by several visitors to the stand.
Nick Redfearn Managing Director said. "We have received some great enquiries during the show which we are confident will lead to new business opportunities. We are especially pleased with the interest show in our Pallet Conveyor range and look forward to working on some new projects in the near future."
Jul 19 2016MCM Overhead Conveyor Systems for Abattoirs
In the first half of this year MCM Conveyor Systems has experienced a high demand from the abattoir and meat processing industry for its overhead chain conveyor systems. MCM Conveyor Systems, a division of Amber Industries ltd, has a long track record and established reputation for manufacturing and supplying very reliable yet low maintenance overhead conveyor systems to abattoirs, either directly or via the abattoir equipment trade.
The operating environment in abattoirs is harsh. Equipment is regularly subjected to low temperatures, high pressure washing and corrosive attack from animal waste and strong chemical cleaning agents. The engineers at MCM Conveyor Systems design and build their abattoir overhead conveyor systems to deal with these extreme conditions. All components, including the track, chain, drive units, lubricators, wiring and control devices are specially designed and selected to ensure the whole conveyor system operates reliably throughout a long lifespan. MCM’s overhead conveyor systems can be supplied with the following features and options:
- Manual or fully automated
- Bi-directional track with tight radius curves to minimise ’system footprint’ where processing lines are constrained by limited available floor space
- Track in either stainless steel or dipped galvanized mild steel
- Product can either be hung directly from the overhead conveyor or alternatively from separate rails in turn pushed by the conveyor
- A selection of chain bearing types depending on specific conditions and budgets, i.e.
i)Fully sealed ‘food’safe’ greased for life bearings,
ii) Full complement bearings
iii) Stainless steel balls
iv) Yellow zinc passivated sintered iron cage
Our in-house teams of mechanical and electrical design engineers give MCM the capability to deliver bespoke conveyor systems to precisely meet individual customer requirements.
Jun 20 2016Sandvik Paint Plant Conveyor
With the planned expansion of the current manufacturing facility at Ballygawley, Sandvik recognised that there was a requirement for a new finishing plant that would include shot blast booths, paint booths, ovens and an automated conveyor system in order to streamline this part of the production process and cope with the constant increasing demand of machines.
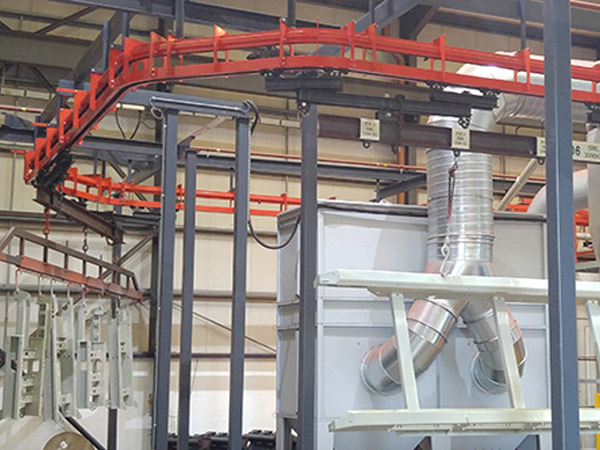
Working closely with the engineers at Sandvik and other associated major contractors, Amber Industries Ltd developed a turnkey solution and was subsequently awarded the contract for the new conveyor system utilising our standard Autotrack 500M Power & Free overhead conveyor.
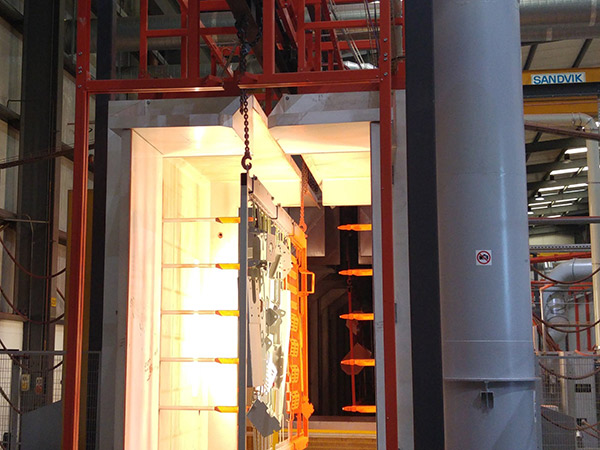
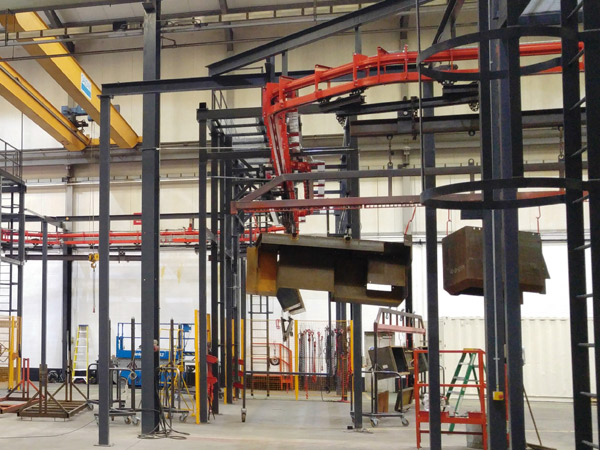
Mar 16 2016Amber Strengthens Electrical & Control Systems
In response to industry demand for greater automation of materials handling/conveyor systems and the resulting need for controls systems with a higher degree of complexity, Amber Industries Ltd has recently strengthened its electrical & control systems department with the recruitment of two additional controls systems engineers.
We are delighted to welcome Scott Hughes and Hans Hofmann to Amber Industries. Both Scott and Hans are based at the company’s head office in Oldham, however the nature of their roles will mean that they will often be on client’s sites commissioning the latest conveyor projects.
Tony Moore, Systems Director of Amber Industries says that the addition of Scott and Hans to the team brings a depth of experience and a level of resource which significantly enhances Amber Industries capability to successfully undertake some of the larger and more complex projects that our clients present us with.
Mar 10 2016Amber Industries Exhibiting at IMHX 2016 Booth 8D10
IMHX is the premier meeting place for the UK’s intralogistics industry. This September will see tens of thousands of supply chain professionals gathering to evaluate cutting edge technologies, explore the latest industry solutions and discuss how to increase efficiencies within supply chain operations. There will also be the opportunity to network with industry colleagues and debate the industry's hottest topics.
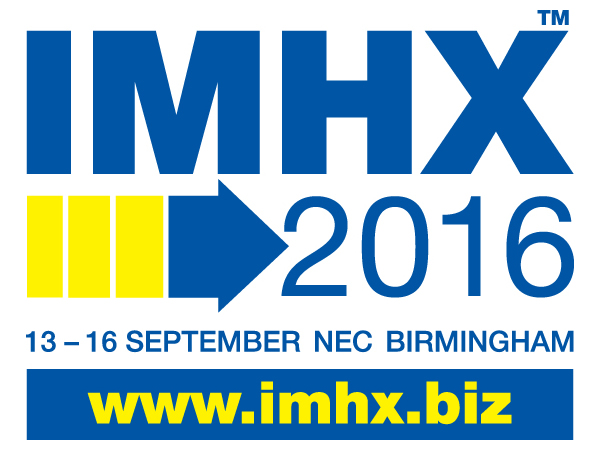
Taking place at the NEC Birmingham from 13th-16th September, demand for stand space has been exceptional and IMHX 2016 will be the biggest and most comprehensive in the show’s history. With over 450 exhibitors, free-to-attend seminars, RTITB Operator of the Year competition arena and an interactive Skills and Apprenticeship zone, IMHX is the only intralogistics event that you need to attend in 2016.
Nov 10 2015Automated Conveyor System For SEW Eurodrive
SEW Eurodrive are globally recognised as market leaders in drive engineering stretching across five continents and employing 14000 people. When their new manufacturing facility at Normanton, West Yorkshire was in the planning, SEW recognised this as an opportunity to introduce an automated conveyor system to service the new paint plant facility that would streamline the existing process for their range of drive equipment.
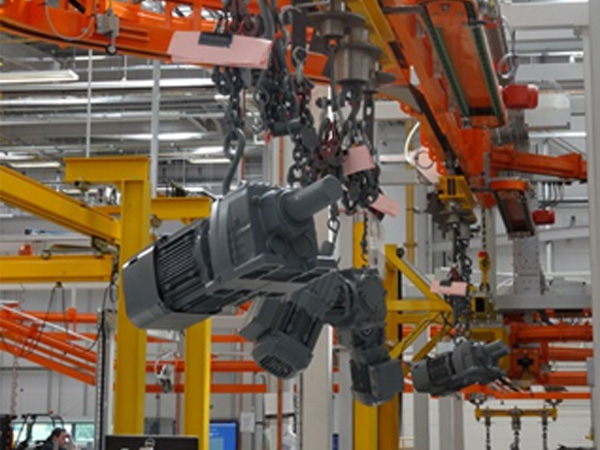
Working closely with the engineers at SEW Eurodrive, Amber Industries Ltd developed a turnkey solution and was subsequently awarded the contract for the new conveyor system utilising our standard Autotrack 500M Power &free overhead conveyor.
The brief given by Sew Eurodrive was that the conveyor had to handle all derivatives of geared motor units ranging from 15kg to 1000kg, These units being loaded at one end of the factory and the system to have the ability for diverting product from daily business and coloured lanes together with a “Fast-Track lane”. The fast track lane that by passes normal daily business is very important to SEW as they pride themselves upon their service of having the ability to deliver to customers on an urgent basis.
There was also the requirement of the conveyor having the capability of raising and lowering product within the spray booth and at the inspection area whilst allowing the operator to rotate the unit during the spray process. A multi height drop section at the inspection area allowed the operator to inspect the product thoroughly prior to despatching to the appropriate unload stations.
Amber Industries Provides An Automated Conveyor System For SEW Eurodrive
In order to achieve all of SEW requirements, the system was designed with 2 loading stations having a stationary trolley set assembly in position that would allow the operator to attach the product onto the trolley load bar support points, smaller products being suspended from any of the rotation units on the load bar, whilst larger product would be suspended from the central rotation point.
The operator at either of the two load stations scans the product(s) and then presses a button at his work station that determines if the loaded trolley is to be routed to normal business, colour or Fast Track. When the trolley arrives at the storage lanes, the conveyor switch point automatically diverts the trolley into the appropriate storage lane. A monitor within the spray booth allows the operator to view the jobs in hand, allowing him to select from the appropriate lane. The Fast Track lane can by-pass accumulating daily business enabling the unit to be painted without being held up by normal business.
With the trolley now in the spray booth, the operator can lower the drop section as required to an ergonomic height due to the differences in product size to allow him to spray all the relevant aspects of the product whilst remaining stationary. The load bar assembly was designed such that the products can be turned through 360 degree during the spraying operation and then locked after the spray operation to maintain correct product orientation. A major benefit of the drop section ensured that lowering of the product could be achieved within a small area compared to that of a conventional conveyor rise and fall.
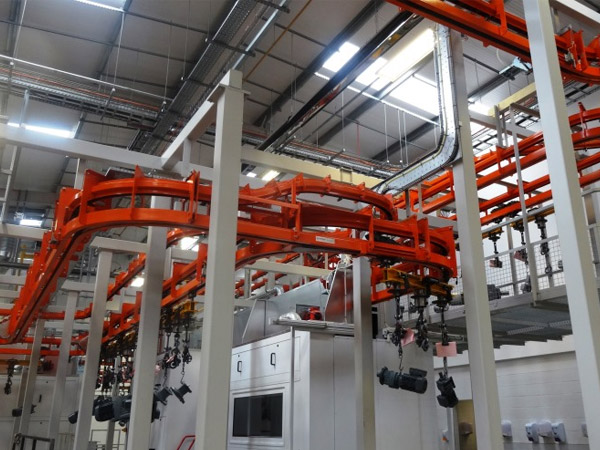
With the paint spray process now complete and the drop section in the raised and locked position, the operator again presses a button that determines once more if the product routing is that of standard daily business or if the trolley route is that of “fast track”. The trolley set that now contains the painted product would automatically be released back into the system where it will dry in the Drying Oven for a stipulated time period and temperature. Products are then automatically accumulated and released out of the dryer once they have been in the oven for the allocated time.
As the overall paint plant facility has automatic opening doors within certain parts of the plant, the electronic controls on the conveyor system have to be synchronised with these elements to avoid clash conditions when opening and closing.
then gets routed to the main dry off oven where again they are accumulated within the oven for another differing stipulated time and temperature. Upon exit of the main curing, the trolley set complete with dried product would then be automatically diverted either into the normal business line or routed to the “fast track” lane.
Products that are deemed for daily business would be diverted into a storage loop which in turn then continues to travel to the multi height inspection drop section, but trolley sets that are deemed as Fast Track (urgent orders) do not enter the normal business loop, these are diverted directly to the inspection drop section. The loaded trolley set is again stationary for the inspection process allowing the operator to raise and lower the product together with rotation through 360 degree for full inspection.
Upon completion of inspection the operator determines if the product is to be transported to unload station 1 or 2. And the inspected unit is now automatically routed to the pre-requisite unload destination. After unloading, the empty trolley sets are routed back to the loading stations. Using state of the art electronics enables the integration of the conveyor system to work in conjunction with other plant and equipment ensuring correct product movement and timings as and when required. Consideration also had to be given to where products passed over gangways, with this in mind and the weights involved, a heavy duty walkable underside guarding was provided where necessary.
Sept 2 2015Amber Industries to exhibit at Surface World 2015
Amber Industries will be exhibiting at Surface World 2015 from September 23rd to 24th at the NEC in Birmingham at Booth number 50. The exhibition is the UK’s only international event dedicated to the surface treatment, product finishing and coatings industry. It provides a major showcase for the very latest technology and developments in this important and expanding area.
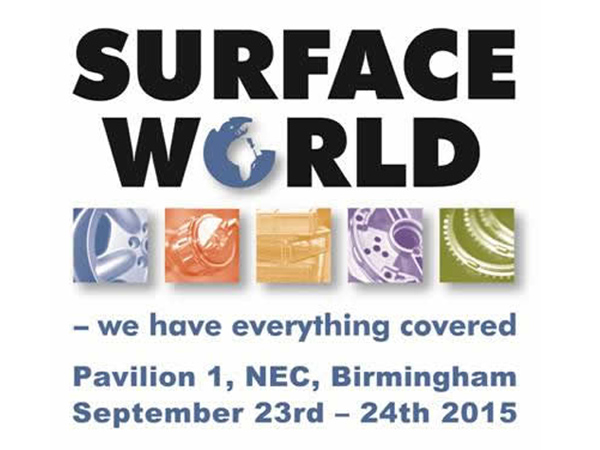
Surface World has just announced five major spray equipment manufacturers will be exhibiting at Surface World 2015. If you have a surface that requires a high standard finish then a visit to Surface World will save you time and money. At the show you will find a wealth of experience on hand to provide solutions to your finishing queries all under one roof, no matter what your requirement or problem, large or small, at Surface World you will find the answer.
Amber Industries are a major supplier of overhead conveyor systems for the painting and finishing industry with thousands of systems installed worldwide. We have a long established reputation for the quality, reliability, durability and competitiveness of our products. We will be exhibiting a static display showing our full range of overhead conveyor systems including our Sidetrack and Power and Free ranges. We look forward to seeing our existing customers and potential new customers at this important exhibition for the industry.
Apr 14 2015Johnston Sweepers Chooses Amber Conveyors
Johnston Sweepers has been manufacturing road sweepers in Dorking, Surrey for more than 75 years, and in that time has become one of the world market leaders in street cleansing vehicles, British designed and built. Johnston exports over 70% of its sweeper production to more than 80 countries worldwide, with exports increasing year-on-year. They are one of the market leaders in their product field with strong positions in the UK, North America, Australia and Middle East as well as other smaller countries throughout the world.
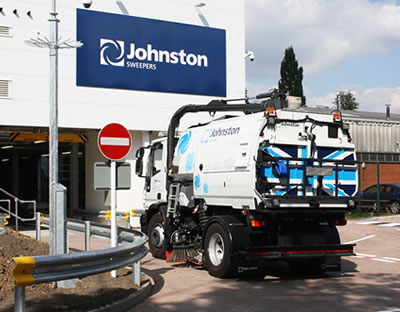
As part of a planned structured review, a new factory wing was built at their Dorking site, an £11m project consolidating all three UK manufacturing plants. The new factory aims to be the most modern sweeper manufacturing facility in Europe, with all-new technology and assembly flow lines for maximum efficiency and quality. Forming part of this new facility, a new finishing plant was commissioned to include shot blast booths, painting booths and the latest paint application equipment, all served by an overhead conveyor system.
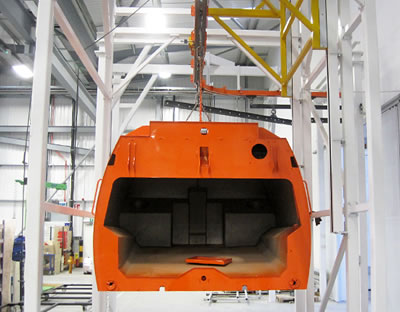
One major aspect of the new handling system was the ability to easily load and unload sweeper bodies, which could weigh up to 2000kg, and to be able to move them manually around the system via a series of switch junction points. The conveyor system proposed by Amber was the ATFT500, with each master load bar connected to four trolleys to carry the sweeper body. The load bar was developed to allow the hook positions to be moved easily to suit each sweeper model.
To test the ease of manoeuvrability around the facility, Amber built a test track within its factory to test the varying loads and invited the Johnston Sweepers project team to test the effort required to pull or push these loads up to the 2000kg level. This gave Johnston Sweepers the confidence that they required to move forward with the installation of the new system. The operation proposed was relatively simple. The sweeper body would be loaded onto the system via a load drop section, where the track would then lower to allow the operator to load the unit. The sweeper body would then be pushed into one of two shot blast booths for manual blasting, before being pushed via switch points into one of four paint application booths.
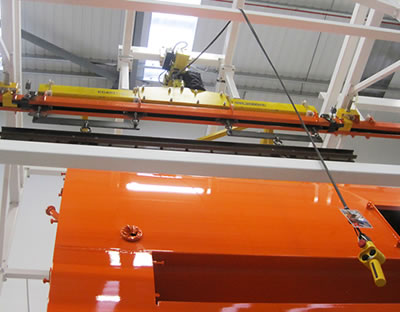
Once the painting and drying operation was complete, the product would be un-loaded via an unload drop sectionpositioned after the final booth and the empty trolley set returned, ready for a new product to enter the system."I was very pleased with the conveyor system installed by Amber Industries and with the professional way that they conducted themselves throughout project" said Amin Ferdowsian, Manufacturing Technology Manager at Johnston Sweepers.
Jan 6 2015Amber Installs Overhead Solution for Moving Rubber
Amber was approached by Fothergill Polycom to provide a method of transporting rubber from the mixers to the rolling mills at their new facility on Drury Lane, Oldham. This method previously utilised a belt conveyor. However, this had proved to be very inefficient. The rubber had a tendency to fall over the edges of the belt and touch the floor, which increased the chance of rejection due to contamination. The steep incline of the existing belt conveyor also meant that the rubber tended to fall back down the belt, so that operators had to intervene on a regular basis to help the transportation process.
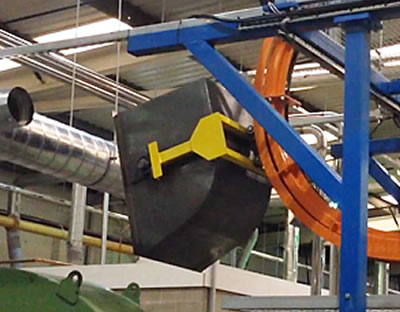
Fothergill Polycom Ltd (formerly Ferguson Polycom Ltd) manufactures and supplies rubber compounds and rubber-coated fabrics from a custom-designed new facility in Oldham, Lancashire. They are the leading niche manufacturer of custom and industry standard black filled and coloured master batches and compounds in cut and continuous sheet form and narrow strip. These are used in a variety of industries and processes, including compression and injection moulding, calendering, coating and extrusion.
Fothergill Polycom Ltd has over 4,000 formulations on file and continues to design and develop compounds and master batches to customer specific requirements, as well as industry standards. Typical applications include automotive mouldings and extrusions, seals for use with water and gases, coatings, calendering and cured sheeting. Both natural and synthetic polymers are processed through their internal or open mill mixers, and they have the flexibility to offer small and single batch requirements, useful for small scale development work or highly-specialised compound requirements.
As part of its on-going programme of investment and continuous improvement, Fothergill Polycom Ltd relocated to new premises just a short distance away, ensuring the location did not inconvenience the workforce, as well as remaining adjacent to the road network in Greater Manchester.
Amber was approached by Fothergill Polycom to provide a method of transporting rubber from the mixers to the rolling mills at their new facility on Drury Lane, Oldham. This method previously utilised a belt conveyor. However, this had proved to be very inefficient. The rubber had a tendency to fall over the edges of the belt and touch the floor, which increased the chance of rejection due to contamination.
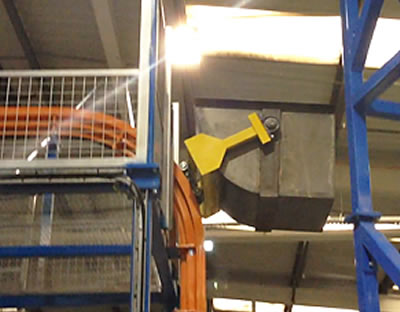
The steep incline of the existing belt conveyor also meant that the rubber tended to fall back down the belt, so that operators had to intervene on a regular basis to help the transportation process. The new location of the mixer meant that the rolling mill was very close, and the angle to deposit the rubber would be even greater at the new site presenting a much greater challenge.
Amber's brief at the Drury Lane facility was to transport the rubber from the mixers to the rolling mills, without the rubber touching the floor, without wastage, without operators having to intervene in pushing the rubber to the rollers, and at the same time giving full access to the rollers from both sides and all in a much more restricted space.
After numerous ideas, Ambers Industries' solution was to create a circuit utilising standard components consisting of straight track, curves and chain, together with a frame to support a bucket, designed to fit beneath the mixer which would hold the rubber. The bucket was designed to remain in the horizontal position beneath the mixer ready to be loaded, as well as during its vertical climb prior to being fixed for the vertical tipping action, ensuring the rubber ejects over the rolling mills. The bucket was also Teflon coated to help prevent the rubber from sticking on discharge.
The overall operation was relatively simple once the routing issues had been overcome. A signal is received from the mixer to say the rubber has been deposited into the bucket, the conveyor starts and the bucket is transported from under the mixer. It then rises vertically to a 180° degree vertical bend sited above the rolling machine, giving ample clearance for the operators to work underneath. The shape of the bucket and the design of the carriage ensures that throughout the journey the bucket remains upright, however, at the vertical bend the bucket tips forward with the conveyor and effectively pours the rubber from the bucket directly into the centre of the rolling mill. Once the bucket is empty, it is then returned to the starting position to wait for the next deposit of rubber.
Oct 10 2014Amber Industries Provide Solution At Internet Fusion
As part of a major investment at their existing warehouse and office facility in Louth, Lincolnshire, Internet Fusion sought a conveyor specialist to help convey their order picking totes from an extensive mezzanine storage area to a ground floor packing line. Amber Industries supplied a range of purpose designed, roller and belt conveyors to facilitate this requirement.
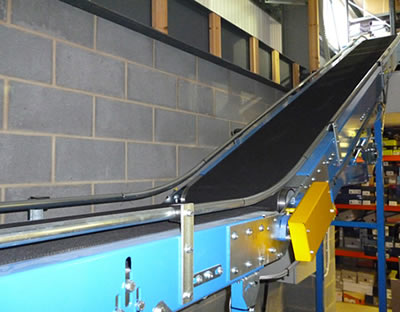
Internet Fusion Ltd specialises in the retail and distribution of high quality products to the UK and Irish markets via extensive online retail and trade networks. Originating as an online retailer with a single webshop in 1999, Internet Fusion now has over 10 market leading online stores supplying thousands of products direct to customers across the UK and Europe.
Alongside the growing retail network Internet Fusion has developed into one of the UK's fastest growing trade distributors being chosen by over 8 global manufacturers to distribute their brands exclusively in the UK and Ireland.
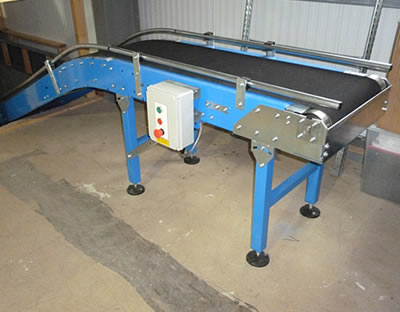
As part of a major investment at their existing warehouse and office facility in Louth, Lincolnshire, Internet Fusion sought a conveyor specialist to help convey their order picking totes from an extensive mezzanine storage area to a ground floor packing line. Amber Industries supplied a range of purpose designed, roller and belt conveyors to facilitate this requirement.
Orders picked into a series of plastic totes are conveyed safely to the ground floor packing area. During their busiest periods up to ten packers remove totes from the upper tier conveyor, pack the orders and place them on to the lower tier conveyor where they are transported to the dispatch area.
Sept 2 2013Surface World Show 2013
MCM Conveyor Systems will be exhibiting at stand number 50 at the forthcoming Surface World Show, held at the Birmingham NEC between 24th and 26th September 2013. MCM Conveyors Systemsare a major supplier of overhead conveyor systems for the painting and finishing industry with thousands of systems installed worldwide. We have a long established reputation for the quality, reliability, durability and competitiveness of our products.
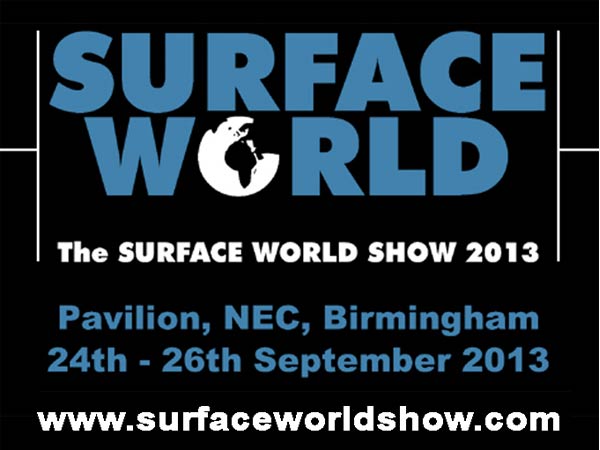
MCM Conveyor Systems will be exhibiting at stand number 50 at the forthcoming Surface World Show, held at the Birmingham NEC between 24th and 26th September 2013. MCM Conveyors Systemsare a major supplier of overhead conveyor systems for the painting and finishing industry with thousands of systems installed worldwide. We have a long established reputation for the quality, reliability, durability and competitiveness of our products. We will be exhibiting a static display showing our full range of overhead conveyor systems including our Sidetrack and Power and Free ranges. We look forward to seeing our existing customers and potential new customers at this important exhibition for the industry.
Mar 10 2013Success for Amber Industries at IMHX 2013
Amber Industries recently exhibited at the IMHX event at the Birmingham NEC. Over 20,000 logistics professionals gathered to learn new ways to improve productivity, cut costs and efficiently manage stock. Amber Industries exhibited both a working floor conveyor system and a static display showcasing its overhead chain conveyor range. The working system started with a powered belt curve which transferred boxes onto a lineshaft straight, before entering a lineshaft powered roller curve, driven from the powered straight.
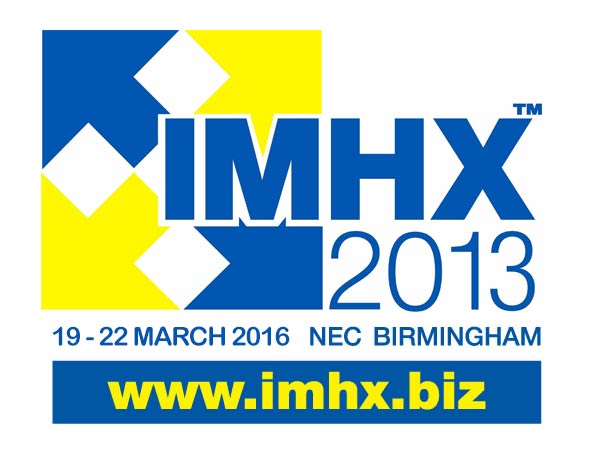
Amber Industries recently exhibited at the IMHX event at the Birmingham NEC. Over 20,000 logistics professionals gathered to learn new ways to improve productivity, cut costs and efficiently manage stock.
Amber Industries exhibited both a working floor conveyor system and a static display showcasing its overhead chain conveyor range. The working system started with a powered belt curve which transferred boxes onto a lineshaft straight, before entering a lineshaft powered roller curve, driven from the powered straight.
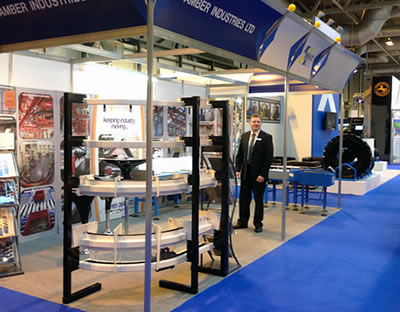
The final conveyor was a section of zero line pressure conveyor, which separate the boxes and can be used to convey fragile items. The system also only runs when there is a position vacant ahead and therefore the motors only run when necessary, saving power.
The system was programmed to reverse with the lineshaft system running at a faster speed than the zero line pressure conveyor, to create a large gap between the boxes. This allows the system to fully demonstrate the zero line pressure concept.
"Potential customers were able to observe the different conveyor operations and gain a greater understanding of the benefits of the different systems" said Kevin Moden, head of sales at Amber Industries. "We have received some great enquiries since the show which we are sure will lead to new business opportunities."
Feb 2 2012Success for Amber Industries at Logistics Link South 2012
Amber Industries recently exhibited at the Logistics Link South show at Sandown Park. Hundreds of logistics professionals gathered to learn new ways to improve productivity, cut costs and efficiently manage stock. Amber Industries exhibited a range of conveyors at the show which included a powered Transportadores Curvos de Banda, a powered belt straight, a lineshaft bend and a powered roller straight.
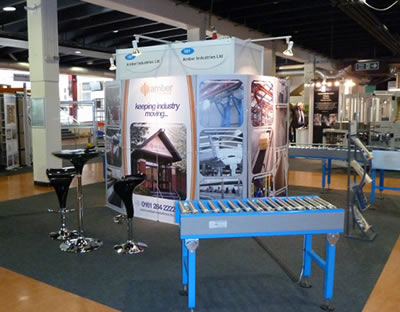
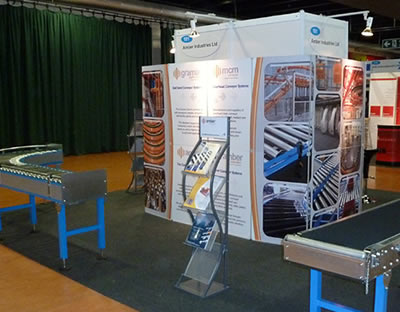
"The conveyors on demonstration gave us a great opportunity to show the quality and workings of our range" said John Spittlehouse, system sales manager at Amber Industries."We have received some great enquiries since the show which we are sure will lead to new business opportunities."
We would like to thank those we met at the show and hope to see you all again soon.

Oct 20 2011Success for MCM Conveyors Systems at the Surface World Show 2011
The Surface World Show is the UK’s bi-annual showcase for the paint finishing industry. MCM Conveyor Systems showcased it's full range of overhead conveyor systems including our Sidetrack and Power and Free ranges. Arguably the UK's leading overhead conveyor manufacturer, MCM Conveyor Systems had a successful three days at the exhibition and considerable interest was shown in all MCMS’s products from a range of different manufacturing sectors.
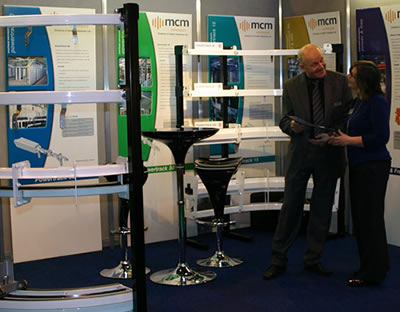
The Surface World Show is the UK’s bi-annual showcase for the paint finishing industry. MCM Conveyor Systems showcased it's full range of overhead conveyor systems including our Sidetrack and Power and Free ranges.
Arguably the UK's leading overhead conveyor manufacturer, MCM Conveyor Systems had a successful three days at the exhibition and considerable interest was shown in all MCMS’s products from a range of different manufacturing sectors. We received many enquiries as a result of the show and are extremely hopeful of obtaining orders.
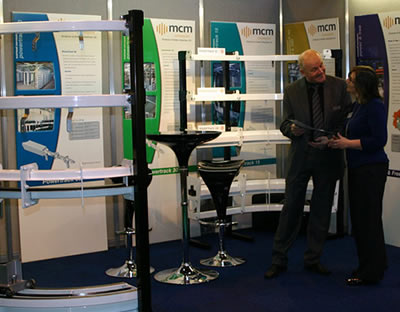
We would like to thank all of our existing and potential new customers for visiting our stand and we hope to see you all again at the next show.
For further information / reader enquiries please contact: Mr. Kevin Moden, Amber Industries, Amber House, Crompton Street, Chadderton, Oldham. OL9 9 AA, Tel: 0161 284 2222, Fax: 0161 627 0075
Jun 6 2010Amber Automation interface conveyors into packaging line at Greencroft Bottling
Leading UK manufacturer Amber Automation successfully completed the installation of a conveying system at Greencroft Bottling Co. Ltd to transfer product from a newly installed tray erector/bottle packing machine into various storage areas.
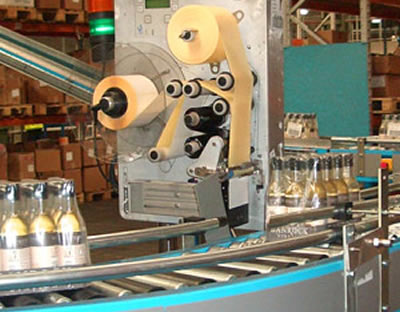
Specialists in bottling wines & spirits from around the world, the Greencroft Bottling Co had previous experience of Amber lineshaft conveyors, which continued to successfully and reliably operate within the Durham based plant. Therefore, Managing Director Mark Satchwell didn’t hesitate to invite Amber Automation to tender for the project.
The contract was to supply a system to interface with automated packaging machinery, conveying complete packs from the out-feed of the inline tray erector/bottle packing machine. On exiting onto Amber lineshaft powered roller conveyor, a pack turner re-orientates the trays through 90 degrees to continue on around a 180 degree bend and up an inclined belt conveyor to a 11m high level lineshaft conveyor. Trays of shrink wrapped bottles are transported at height around a 90 degree bend and can continue along the new line or be transferred down onto one of two existing high level conveyors. A declining gravity conveyor section can be manually positioned (up/down) to transfer product downwards to where a manual diverter blade merges transported goods on to one of the two existing conveyors.
The Managing Director of Greencroft Bottling Co. Mark Satchwell reported “The new conveyor system was part of an investment made in order to service a new contract for a well known wine company. As we had been more than satisfied with the performance of some existing Amber lineshaft on site, we invited Amber Automation to tender for the contract that was also challenging, because it had a short delivery time.
The contract was eventually awarded to Amber Automation in January this year, based on a competitive price, past experience and the fact they are UK based. The conveyors were supplied, installed and commissioned by the 2nd March 2009. Working closely with Greencroft Bottling Co. engineers, the system was professionally installed with minimum disruption to the ongoing business and was executed on time and to budget – a good job well done!
For further information / reader enquiries please contact: Amber Automation, Amber House, Crompton Street, Chadderton, Oldham, OL9 9 AA, Tel: 0161 284 2222, Fax: 0161 627 0075
For further editorial information please contact: Mr Eddie Collins, Director. B.C. Marketing Ltd, 7 Eastway Business Village, Olivers Place, Fulwood, Preston. PR2 9WT. Tel: 01772 654654, Fax: 01772 652233.
Oct 4 2009MCM Conveyors Systems At The Surface World Show 2009
MCM Conveyor Systems will be exhibiting on stand number 52 at the forthcoming Surface World Show 2009 between 27th and 29th October at the NEC in Birmingham. MCM Conveyors Systemsare a major supplier of overhead conveyor systems for the painting and finishing industry with thousands of systems installed worldwide. We have a long established reputation for the quality, reliability, durability and competitiveness of our products.
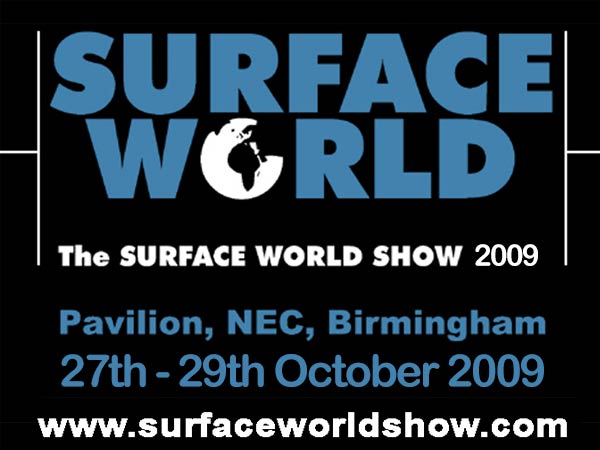
We will be exhibiting a static display showing our full range of overhead conveyor systems including our Sidetrack and Power and Free ranges. We look forward to seeing our existing customers and potential new customers at this important exhibition for the industry.
Sept 10 2009Success for Amber at the PPMA 2009
The PPMA Show is the UK’s annual showcase for processing and packaging machinery. Amber showcased its powered accumulation conveyor and one of its Transportadores Curvos de Banda used for conveying totes and similar boxed items.
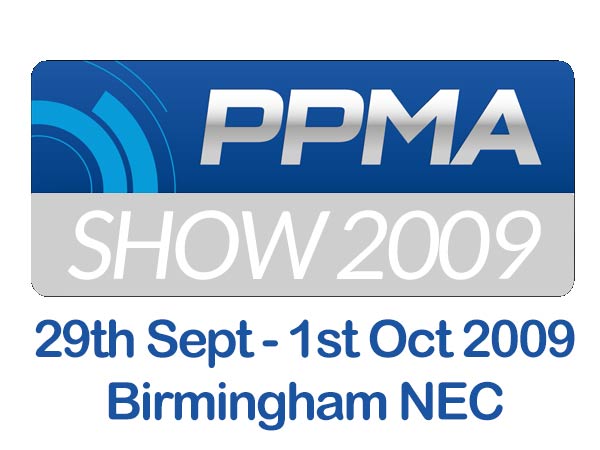
The exhibition catered to all the major UK Sectores industriales; from food & drink and household products through to pharmaceuticals, cosmetics and chemicals, incorporating the widest range of machinery.
Amber Industries had a successful three days at the exhibition, and considerable interest was shown in all Amber’s products from a range of different Sectores industriales. We received many live enquiries as a result of the show and are extremely hopeful of obtaining orders.
We would like to thank all of our existing and potential new customers for visiting our stand and we hope to see you all again next year.
Mar 7 2009Gramac Quartz Systems at the Passenger Terminal Expo 2009
Gramac Quartz Systems will be exhibiting on stand number 1950 at the forthcoming Passenger Terminal Expo 2009 at the end of March. Gramac Quartz are a major supplier of Transportadores Curvos de Banda and merges to the baggage handling industry with thousands of units installed worldwide in many international airports. We have a long established reputation for the quality, reliability, durability and competitiveness of our products.
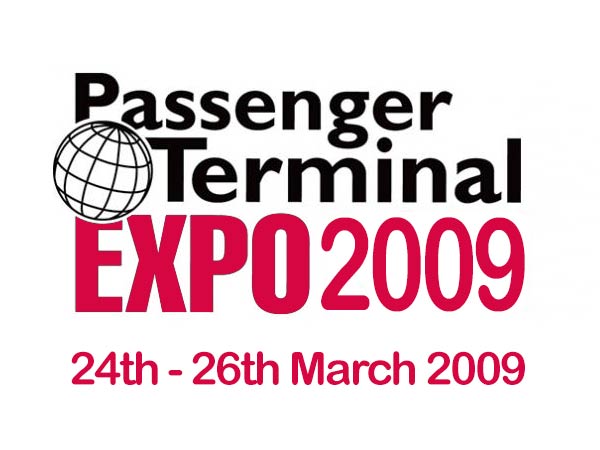
Gramac Quartz Systems will be exhibiting on stand number 1950 at the forthcoming Passenger Terminal Expo 2009 at the end of March. Gramac Quartz are a major supplier of Transportadores Curvos de Banda and merges to the baggage handling industry with thousands of units installed worldwide in many international airports. We have a long established reputation for the quality, reliability, durability and competitiveness of our products. All of the Gramac Quartz Transportadores Curvos de Banda and merge products are manufactured from the most robust materials and continue to operate trouble-free in airports throughout the world.
We look forward to seeing our existing customers and potential new customers at this important exhibition for the industry.
Jan 1 2009MCM Transportadores aéreos Provide a Solution for Weir Valves
When Weir Valves & Controls UK Ltd looked at improving the efficiency and handling capacity of their valve painting system, through shot blasting, a paint booth and curing oven they invited MCM Conveyors Systemsof Oldham to tender for the project. Mr Philip Dollin of Weir Valves & Controls UK Ltd commented,” After reviewing a number of tender proposals, overhead conveyor specialist MCM Conveyors Systemswas appointed to provide a total handling solution. Apart from being competitive, MCM Conveyors Systemsclearly demonstrated that they understood our requirements and could also offer comprehensive after sales service, which we believe is essential in committing to capital investment projects.”
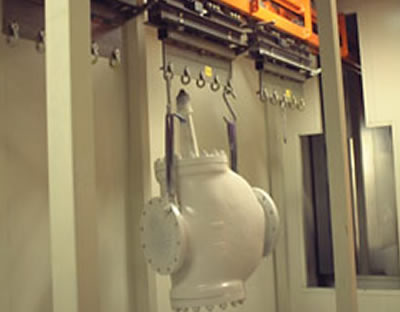
The system was designed to give maximum flexibility and efficiency with single products up to 2000kg. being loaded on to bespoke rotating, multi-jig flightbars, suspended from an MCM Autotrack 500 (AT500) overhead ‘Power + Free’ system in order to be conveyed around a circuit to designated un-load / finishing stations.
Individual Weir valves are loaded by manually operating a pendant raise/lower control to lower the carriage to an ergonomical height to allow product slings to be attached to the valve. Various data is assigned to each loadbar assembly via an electronic tag, which is used at the booth and oven areas to determine product routing, paint finish and cure times. Once the slings are safely attached and the valve masked, the operative will commence to raise the drop section carriage to a final 200mm, at which point the vertical travel will be completed automatically through a PLC that monitors all controls and movement within the system. A release button activates and frees the load bar to transport the valve to accumulate at the shot blast entrance, allowing an empty loadbar assembly to enter the load/unloading station.
As a safety precaution, a product load gate was fitted to detect and ensure that the work envelope is not exceeded and in the case of an oversized or mis-aligned product being loaded, the conveyor will initiate an alarm and stop. The loadbar assembly enters the enclosure as and when an empty position is detected by the PLC and an operative has activated a ‘product call’ button. On completion of the shot blasting, a ‘product release’ button is activated by the shot blasting operative to automatically open the machine doors for the product to be conveyed forward to accumulate at the painting booth.
Following the same entrance procedure, once in the paint booth the multi-jig flightbar is automatically unlocked, via a push button control and allows the operative to rotate the product during painting. On completion, the flightbar is re-locked in its inline position on the MCM overhead conveyor. As a precaution, a special guide is fitted to re-orientate and lock the rotating flightbar if the operative has overlooked the procedure. However, if for any reason the flightbar is mis-aligned beyond an acceptable angle, a load gate detects the position and automatically initiates an alarm and stops the conveyor.
Utilising the Read/Write electronic tag system, the control system automatically provides operatives with process information including paint colour, number of paint coats and curing times. The Read/Write system also allows additional information to be added to individual loadbar assemblies by Weir Valves & Controls. All controls and activating buttons within the booth enclosures are intrinsically safe.
After valves leave the paint booth they accumulate in line on the MCM overhead conveyor. A switch gate detects curing times (3 or 6 hour) and sorts product to different conveying lines to pass through the oven. On leaving the oven, products are merged into one line and are either re-circulated for multi-painting or are automatically routed towards the load/unloading station to be lowered onto an awaiting pallet. The empty flightbar is then re-loaded with product to re-commence the painting cycle.
The system has now been successfully installed and is operating trouble free. Weir Valves & Controls UK reported, “MCM Conveyors Systemsworked very closely with our Project Team and we developed a good working relationship. MCM’s commitment in delivering this project could not be faulted and the installation was completed on time and within budget. Once installed, MCM provided operative training for our people and highlighted basic maintenance procedures. It was important that the line offered maximum flexibility to complete valve painting to customers specific individual requirements. The system has operated successfully and reliably since installed and Weir Valves & Controls UK appointed MCM to provide an ongoing scheduled service and maintenance package. As a result of this success, and based on the above experience I would not hesitate to recommend them”.
Dec 10 2008Amber Automation Win With Practical System Design
Amber Automation was commissioned to design, manufacture and install a warehouse conveying system for leading computer software and hardware distribution company, Bell Microproducts Europe Ltd. Amber’s proposed design, cost effectively incorporated the use of an existing lineshaft carousel conveyor with new powered roller conveyors and full electrical controls to convey packed cardboard boxes from the current sixteen packing stations, to a new despatch unload area.
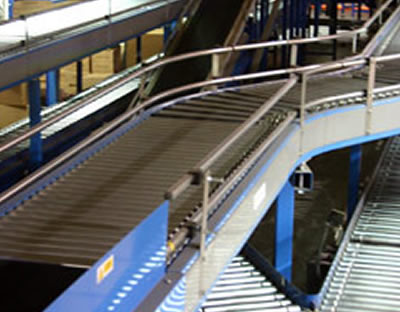
Awarded the contract against stiff competition and previous suppliers to Bell Microproducts, a spokesman for the customer commented, “Amber Automations proposal not only met our project criteria to the full, it presented us with a very competitive and practical tender, which included the integration of new and existing equipment, with minimal disruption to our ongoing business requirements. The project was completed on time, to agreed budget and has been successfully operating trouble free.“
Practical & Cost Effective
Amber Automation's design proposal incorporated a new lineshaft carousel conveyor with a lowered existing roller bed, which enabled order pick boxes with raised flaps to be transported underneath the proposed new conveyor. Amber also supplied and installed additional un-powered infill rollers to provide a closer pitch to ensure maximum flexibility in handling cartons of various sizes.
Operators at the 16 packing stations remove cartons containing fulfilled orders from the lower carousel for final checking and sealing. These are then returned on to the new top tier LS50 lineshaft roller conveyor manufactured by Amber and transported to a despatch area via lineshaft and inclined / decline belt conveyors in order to maintain a clear gangway access. Cartons continue to the unload area with accumulation for manual scanning and unloading.
To ensure a good ergonomic working position for packers, purpose built new modular work platforms were positioned and bolted together in order to ensure the top tier was at a comfortable and acceptable working height. Also, two side mounted drive motors were unobtrusively fitted to the new conveyors to ensure total clearance for cartons being transported at the lower level.
The new warehouse conveying system operates on a nine hour shift, handling cardboard cartons up to a maximum weight of 20kg. and is fully controlled from Amber’s main system electrical control panel. Emergency pull cords are positioned on the side of the conveyors and ‘line full switches’ strategically positioned at the exit of the inclined/ start of the declined belt conveyors as a safety precautionary measure.
The system continues to reliably meet the handling needs of the customer.
Nov 4 2008MCM Provide Handling Solutions for Electrolux
When Electrolux looked at improving the handling and transportation of cooker component parts from their press area, through a pre-treatment facility and returning them to numerous enamelling application un-load stations, they invited MCM Conveyors Systemsof Oldham to tender for the project as they had previously undertaken projects at the Spennymoor plant back in the 1990’s. After reviewing several tender proposals, overhead conveyor specialist MCM Conveyors Systemswas appointed to provide a total handling solution.
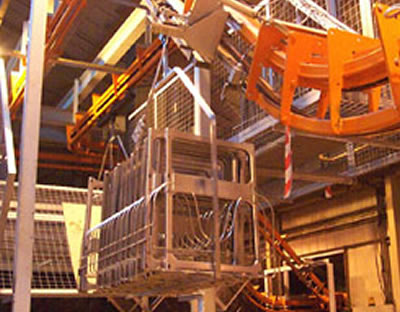
MCM Autotrack 100 Power and Free Solution
The whole system was designed to give maximum flexibility and efficiency with bespoke basket type jigs suspended from load bars, attached to overhead ‘Power + Free’ trolley sets and conveyed around a series of process/ delivery conveyor circuits to designated un-load stations.
Practical & Cost Effective
From three loading stations, product is routed from one building to an adjacent unit over a 6m gangway, feeding down to five enamel application booths (1-5). Each trolley set carries a common single jig, which is capable of holding a variety of components in differing quantities according to size. The average number of components carried in each jig is 16 and grouped to five major classifications according to destination. As a norm components are conveyed through a pre-treatment plant and dry-off oven for product cleaning, but there is also a number of component classifications that bye-pass this stage and feed directly to the Enamel Application booths.
Working closely with Electrolux management, MCM Conveyors Systemsdesigned an identification and routing system based on the use of ‘coded flags’ located on the trolley by two captive pegs and read by strategically positioned code readers. It is a very simple and reliable system, requiring manual setting of each trolley / jig. This provides the following identification and routing information to the PLC - components requiring pre-treatment or not; enamel application un-load stations destination (1/2/3/4/ or 5) and jig loaded or empty. The system design enabled one, two or all three loading stations to be operated. To facilitate the simultaneous operation of all three load stations, a buffer store of four trolley sets accumulate at each station to ensure continuous operations and maximum line efficiency.
After leaving the loading stations, trolleys pass through a small buffer store and then through a code reader where they are directed via a switch junction and power transfer, either into the pre-treatment plant or through the bye-pass. The normal route would be through the pre-treatment plant, where trolleys are transferred onto a slower conveyor for processing through pre- treatment and the dry off oven.
After processing, they are returned back onto the high speed delivery conveyor, where they pass through three small storage banks before being transferred onto a Re-Circulating Conveyor. This has a dual function to deliver to the five individual ‘Enamel Application Unload Stations’ and also acts as a storage facility for both empty and loaded trolleys as the system dictates. The system has the control and capacity to cope with any process back-up, diverting to storage banks or, re-circulating via loading stations as required - at which point, they can be off-loaded for palletising and delivery by fork lift truck should more drastic measures be required.
Empty trolleys are released from the Enamel Application Unloading Stations by an operator push button, returning on the Re-Circulating Conveyor back to the loading stations as required.
The system has now been successfully installed and is operating trouble free. A spokesman for Electrolux reported, “MCM Conveyors Systemsworked very closely with our Project Team and we developed a good working relationship. MCM’s commitment in delivering this project could not be faulted and the installation was completed on time and within budget.
It was important that production was not disrupted and MCM Conveyors Systemsworked through a production shut down period to successfully complete the project within the strict time slot available. Electrolux is now operating the system on double shifts and the efficiencies in handling are there to be seen.
As a result of this success, further smaller material handling projects have been undertaken by MCM for Electrolux, and based on the above experience would not hesitate to recommend them”.
Oct 3 2008MCM Overhead Conveyor Installations at Mitras Automotive (UK) Ltd
MCM Conveyors Systemshas completed the fourth of a series of overhead conveyor installations which have vastly improved storage and handling efficiencies at Mitras Automotive (UK)’s Winsford manufacturing plant over the last two years.
-ltd.jpg)
Mitras manufactures specialised resin moulded components for the automotive industry. Major clients include Ford, Vauxhall, Renault and ERF. Components are produced in relatively large volumes by a compression moulding technique, prior to being assembled as necessary and finally painted to the customer’s specification.
Replacing floor space storage and forklift transportation, MCM has installed four separate systems to improve storage and handling of components during production.
The first installation constituted an MCM Powertrack 30 system with a total overall length of approx 300 m, which carries Ford Transit front panels from the moulding area to the paint line conveyor. Components are manually hung onto purpose designed carriers on the system. The track then rises to high level and runs down the centre of the factory prior to descending to low level where the components are manually transferred to the paint line conveyor. In view of the total loading, the system has dual drives and all the high level runs of track have safety underguarding.
The second installation was a Powertrack 30 system arranged in a small loop configuration to convey front panels for the new Renault van between the various moulding and assembly stages. The components are placed onto purpose designed carriers at 915 mm pitches at the moulding station, for subsequent transfer to the riveting operations at a production rate of 72 components per hour. Because of extreme space limitations, the use of an overhead conveyor meant that the delivery and return carriers could pass within a gap of just 900 mm between the production machines.
Thirdly, a Powertrack 100 system was installed to store and transfer Vauxhall Frontera roof canopies from the trimming operation to the paint line. Two products are manually placed on each carrier. The track rises to high level above a mezzanine floor, prior to descending back to low level where the components are transferred to the paint line conveyor.
The system has an overall length of 110 m and has a storage capacity of 96 components. This enables components to be manufactured in batches and finally finished to the customer’s requirements.
-ltd-image.jpg)
A variable speed facility ensures that the optimum speed can be set according to whether the system is being loaded or unloaded.
The final system installed was a Powertrack 30 system to transfer Land Rover roof spoilers from the moulding lines to the paint line conveyor. Again components are loaded and unloaded manually at ground level and the track then rises to high level, to run alongside the Powertrack 100 system. The products are placed onto purpose designed carriers fitted at 2,058 mm pitches, giving a total storage capacity in excess of 1,300 components.
In view of the overall system length of 236 m dual drives with full variable speed control are fitted to cater for the relatively high total loading. All the systems were installed without disruption to the client’s production.
Mitras Automotive (UK) Engineering Manager Carl Kettle said: “The MCM systems have made a massive difference to our storage efficiency during production. Combining both storage and transportation, the systems have freed up massive amounts of floor space, and throughput is now definitely faster. There is also less product damage and the whole operation is now much more streamlined and efficient. It’s a vast improvement over the old methods, without a shadow of a doubt.
“As well as the obvious technical expertise of the company, we were also very impressed by the lead time offered by MCM, as well as the fact that they were able to complete the installation without disruption to existing production. After the success of the first installation, we had no hesitation in calling on them to complete the second third and fourth installations, which have proved just as worthwhile.”
Sep 16 2008Amber Automation Provide a Boost for Order Picking at UniChem
UniChem a leading distributor and wholesaler of pharmaceutical, medical and health and beauty products, recently awarded Amber Industries the contract to supply and install a powered roller conveyor system in its Swansea based delivery centre to improve order picking efficiency, reduce manual handling and improve the flow of products in tote boxes through to dispatch. With a growing demand for UniChem’s high level of service, with twice daily delivery to pharmacies and dispensing doctors in the area, it was important that the system was designed to meet future handling capacities required.
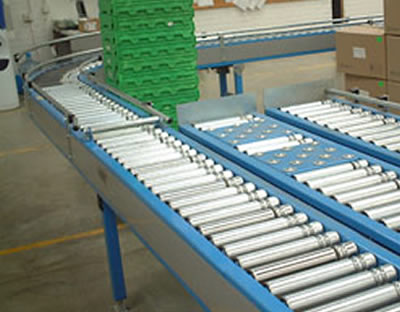
With a growing demand for UniChem’s high level of service, with twice daily delivery to pharmacies and dispensing doctors in the area, it was important that the system was designed to meet future handling capacities required.
UniChem warehouse manager, Paul Stephens reported, “Against stiff competition, we finally selected Amber Industries because they demonstrated a clear under standing of our needs. Ambers’s business-like approach and prompt response gave us confidence, as well as being supported by a competitive tender.”
Utilising Amber’s lineshaft modules provided a versatile and economical conveying system for handling orders collected and placed in tote boxes, providing the customer with a very cost effective and viable materials handling solution. Kevin Moden, of Amber Industries commented, “As a conveyor manufacturer, we had the flexibility and capability to quickly respond to UniChem’s requirements, providing a ‘one stop service’, designing, building and installing the system on time and with minimum disruption to the ongoing business.”
Integrating the System
The old system had to be quickly and safely stripped out between the scheduled order picking times, which took place at a.m (8 – 11) and p.m. (2 – 4), to ensure that van deliveries to UniChem customers was not disrupted. The new conveyor configuration ran parallel with three picking faces and included allocated stations for selected goods to be loaded into tote boxes.

On completion of order picking at face 1, the tote box could be manually pushed on ball transfer tables over the main conveying line, onto an adjacent lane running parallel to order picking face 2. If an order does not require product from face 2, the tote box can be released to dispatch or forwarded on the main powered central roller lane to stations on order pick face 3. On completion of order picking from face 3, the tote boxes are manually transferred onto the main delivery conveying line feeding packing stations for checking, sealing and labeling.
Unfortunately, the routing of the conveyor crosses a main gangway and therefore for safety reasons and access, Amber overcame this problem by designing and installing a pair of double personnel gates. These gates can be easily lifted/ lowered to provide adequate access for both personnel and pallet trucks and are slave driven from the next adjacent up-line conveyor section.
Sealed cartons are allowed to accumulate on end of line, standard gravity roller sections before being off-loaded into their specific warehouse allocations.
UniChem warehouse manager, Mr. Paul Stephens commented, “Both Amber and I worked closely to ensure that the project was completed with minimum disruption, and this was completed on time and within budget. The system has been working successfully and has given us greater handling capacity; order fulfillment is quicker and ensures we are geared to meet the ongoing increase in business.
Aug 1 2008Reilor Logistics recently improve handling with Amber Automation
A long established company and market leader in the design and manufacture of home improvements and pet products, Reilor Logistics recently awarded Amber Automation the contract to supply and install a powered roller, carton handling system to transport goods from assembly areas to the warehouse. Reilor’s Logistic Manager Gary Reid reported, “Despite the competition, we selected Amber Automation above other potential suppliers as they demonstrated a clear understanding of Reilor’s requirements. With a tight window to supply and install the conveyors, Amber’s business-like approach and prompt response gave us confidence, as well as being supported by a competitive project price.”

Reilor’s Logistic Manager Gary Reid reported, “ Despite the competition, we selected Amber Industries above other potential suppliers as they demonstrated a clear understanding of Reilor’s requirements. With a tight window to supply and install the conveyors, Amber’s business-like approach and prompt response gave us confidence, as well as being supported by a competitive project price.”
Utilising Amber’s lineshaft modules provided a versatile and economical conveying and accumulating solution for handling cartons, providing the customer with a very cost effective and viable materials handling solution. Mark Adams, Sales Director of Amber Conveyors commented, “As a conveyor manufacturer we had the flexibility and capability to quickly respond to Reilor’s needs, building product and installing the system within the critical deadlines. Over the years, being able to provide a ‘one stop service’ has often clinched contracts as customers save time and expense on paperwork and more importantly, avoid having to negotiate and liaise with other supplier companies.”
Integrating a System
An existing line was already being utilised to transport assembled goods to a line end, where they were manually transported via hand pallet trucks to the warehouse storage area. The existing system transferred the packages through a carton sealer, operating at a speed of approximately 6 packs per minute.
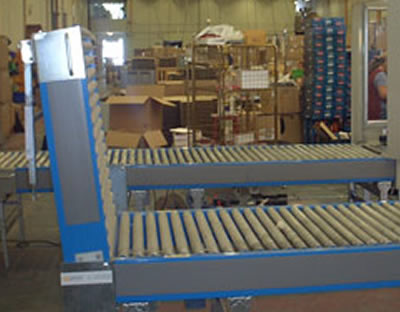
The new conveyor configuration allows for a completely new line feeding from a second assembly area, together with the existing line. A new case sealer operating at 17 packs per minute was also integrated into the revised conveyor layout.
Twenty two packing stations are strategically positioned alongside the two conveyor lines (new & existing), from where fulfilled orders are packed and transferred onto the main delivery conveying lines feeding the case sealers. Packages ranging from 760 Lg x 595 W x 556 H (max.) to 180 Lg x 120 W x 102 H (min.) pass along both of the conveyor lines.
Once sealed, cartons are routed towards the warehouse area, where a bar coded label is scanned and details logged into a warehouse management system (WMS). To ensure maximum handling efficiencies, a pneumatic pusher unit is positioned just after the bar code scanners on each line to reject cart ons if a mis-read occurs.
Unfortunately, the routing of the conveyors pass across a main gangway which could not be bridged via incline/decline belts due to space constraints. Therefore, for safety reasons and access, Amber overcame this problem by designing and installing a pair of double personnel gates. These gates can be easily lifted/ lowered to provide adequate access for both personnel and manual pallet trucks and are slave driven from the next adjacent up-line conveyor section.
Sealed cartons are allowed to accumulate on end of line, standard gravity roller sections before being off-loaded and palletised into their specific warehouse allocation.
Gary Reid, Reilor’s Logistics Manager commented, “Both Amber and I worked together very closely to ensure that the project function, layout, programme timing and budget were achieved. I can now confirm, that the whole system was designed, manufactured and installed by Amber Industries within 4 weeks from placement of the order and has since been working reliably and without any problems.”